Lessons learned from a Deep Energy Retrofit —
By Nate Adams —
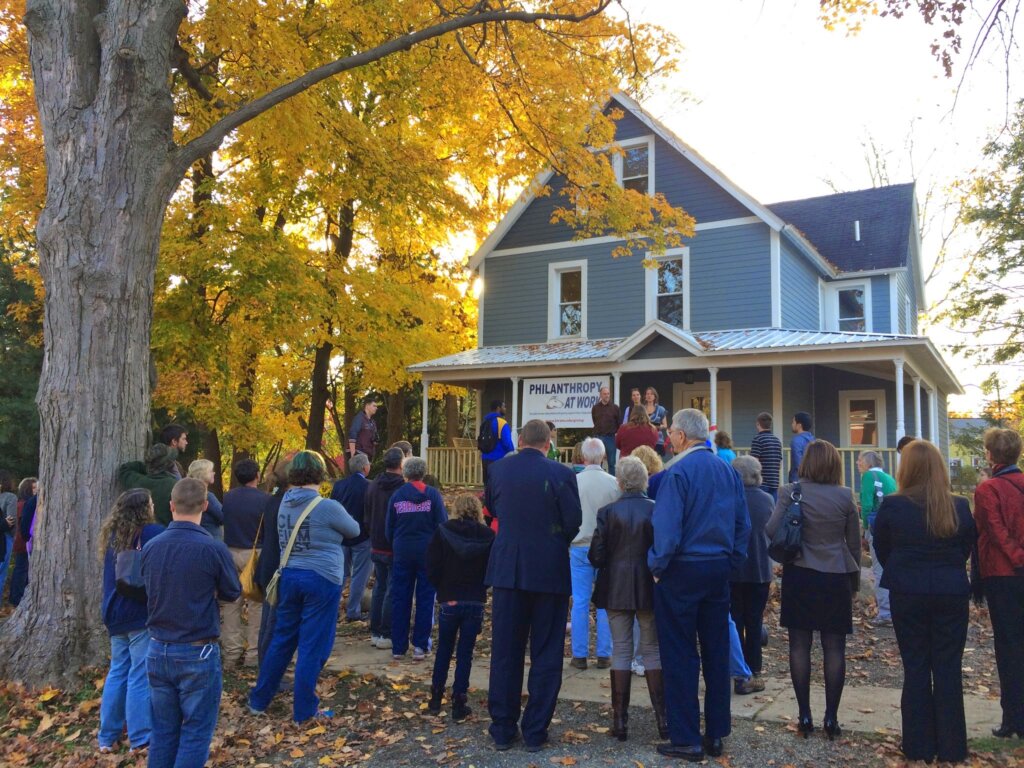
Want to know something crazy about the deep energy retrofit of this building? It uses 35-45% more energy than one of our much less deep projects. That’s one of the things we learned from the Hiram College TREE House project.
Last time we talked about lessons learned about the dust and dehumidification air quality challenges, the comfort challenges caused by fresh air being introduced without being heated or cooling in the classroom, the second floor overheating because of closed office doors with mini split heads in them, and cooling challenges caused by multi-head mini split heat pumps.
These are all pretty common practices in deep energy retrofits, ones that we challenge with our typical projects. That doesn’t mean either is right or wrong, but the more you understand, the better the job you can do on design on your own projects. In the case of the TREE House, a little more thought into placement of the heads and a larger, higher performance mini split heat pump could have changed the results a lot.
This time we’ll compare two of our projects looking at energy use, insulation, and HVAC.
Energy Use
I already dropped the bombshell, this deep energy retrofit got its butt kicked by a much simpler project. Here’s the 2018 usage for the TREE House, 19,500 kilowatt hours.
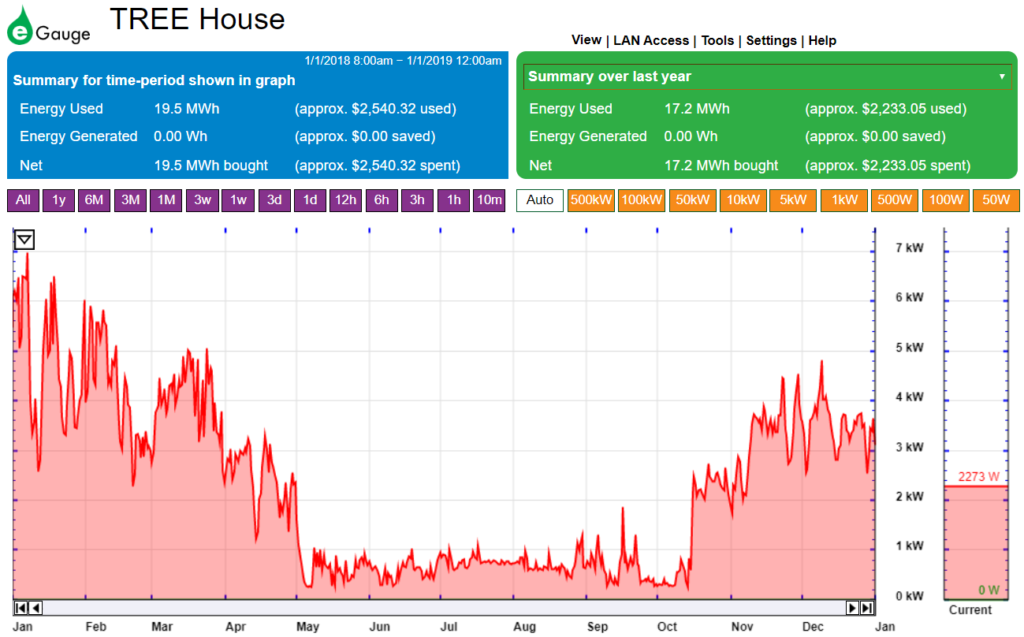
Winter looms large as you might expect, January and February are the coldest months here in Cleveland. Note that despite school starting 6 weeks earlier, usage doesn’t tick up until mid-October when the weather turned. This indicates that occupants don’t affect usage much.
1918 House of the Future Project
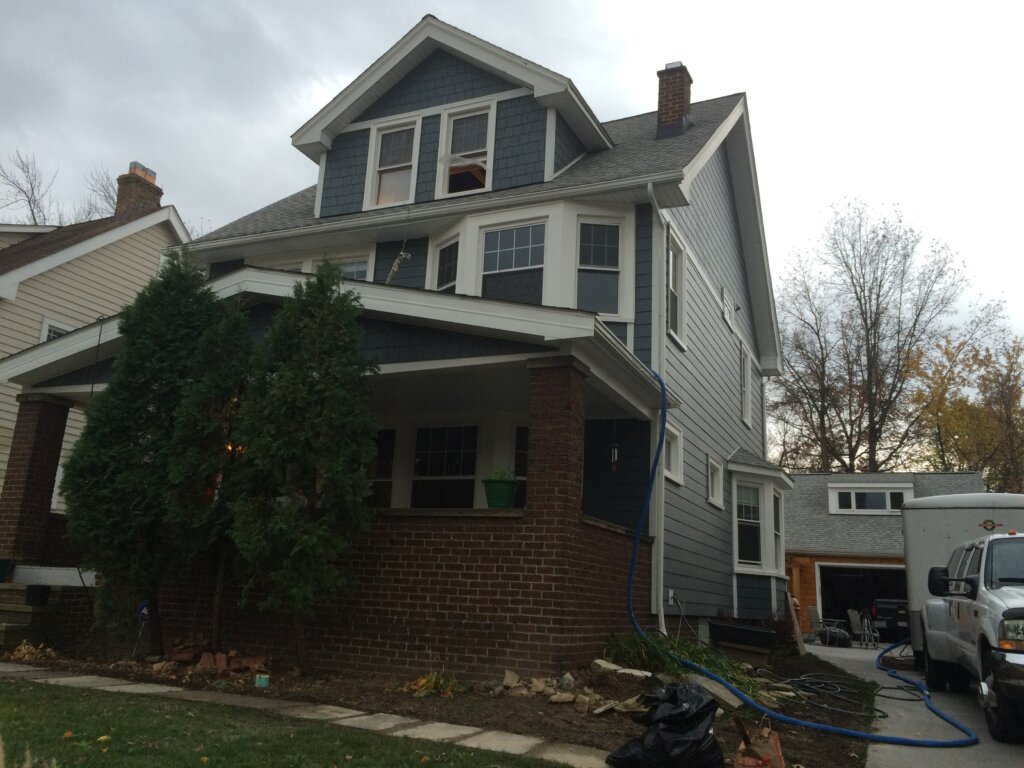
Now let’s look at the 1918 House of the Future project. You can read much more about both projects in the highly detailed case studies at energysmartohio.com. The 1890 and 1900 case studies are also electrifications, we’re presently working on electrifications 11 and 12 – heat pumps work well even in cold climates.
The usage data for this house is from the Sense energy monitor, check out my YouTube channel for a more detailed look at both of these monitors.
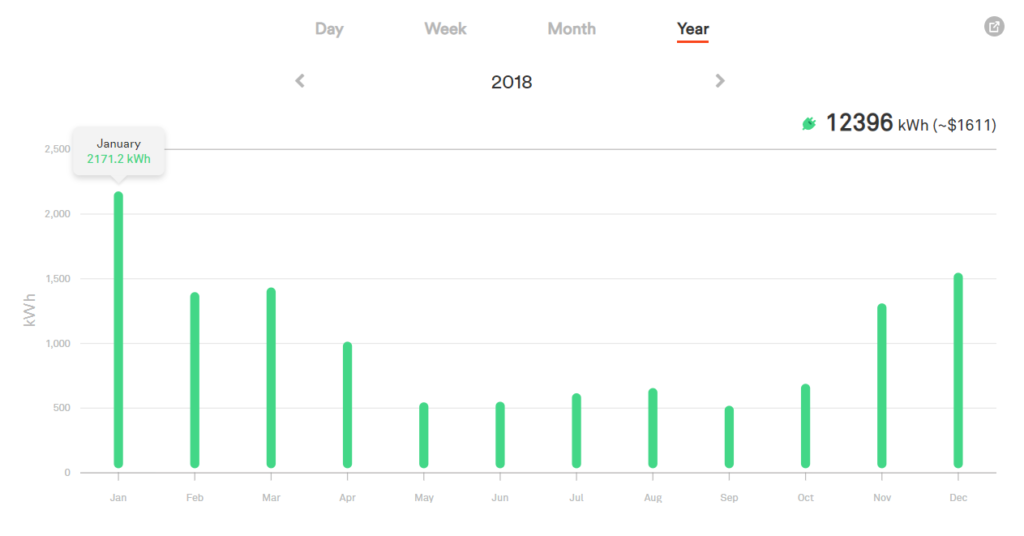
Here’s a high-level comparison of the overall projects, then we’ll dig deeper.
Project | Budget | Sq Feet | Year built | 2018 kWh Usage | HVAC Size (BTU/h) | Blower Door cfm50 | Wall R-value | Attic R-Value | Basement R-value |
Tree House | $150K* | 2000 | ~1900 | 19,500 | 45,000** | 980 | 30 | 70 | 50 |
1918 House of the Future | $40K | 1800 | 1918 | 12,400 | 36,000*** | 1820 | 13 | 25 | 5 |
* Total budget including interior upgrades. $50K for replacing foundation.
** 30,000 BTU multi split heat pump plus 15,000 BTU electric water heater.
*** Plus, 15kw backup heat as needed, another 50,000 BTUs.
Note the drastic difference between energy use. It’s been consistent, the TREE House uses 35-45% more than the 1918 House of the Future despite being only 10% larger and having a far better insulation package on paper. This is pretty wild because no one actually lives at the TREE House, so there is almost no hot water or cooking usage, and lighting usage is presumably lower because it’s needed less during daylight working hours.
Let’s dig deeper into the projects.
The TREE House Insulation Package
I have to say, the insulation package is intense:
- Foundation: The foundation was missing footers under much of it and had 5 different types of foundation. The decision was made to replace it with insulated concrete forms rated at R-50.
- Walls: 3” recycled polyisocyanurate foam board was put over the existing siding. I dense packed the walls from the inside with cellulose. The foam board was covered with Hardi Board siding.
- Attic: 3” foam board over attic floor with taped seams. Edges were spray foamed to seal tops of walls. I blew R-60 cellulose on top of that.
- Windows: Existing double pane.
During the design charettes for the TREE House, we had advocated against doing exterior insulation, we thought it was too costly for the benefits. I don’t know what it models for this house, but on my old house a $75K exterior insulation job modeled $250/year in savings. That said, the new siding does make the house very attractive, where it used to be rather dumpy looking.
1918 House of the Future Insulation Package
- Foundation: 2” closed cell spray foam in rim joists. 2” spray foam on selected walls, about 20% of total basement wall area. R-14
- Walls: Dense packed cellulose, R-13.
- Attic: 3.5” closed cell spray foam on roof deck, R-21-25. 2” closed cell on gable ends, R-14. Yep, that’s it.
- Windows: Double pane Low-E
This house got exactly what we were advocating for in the TREE House – a foamed roof deck to create conditioned storage, dense packed walls, and a standard (albeit very high performance) heat pump to replace the furnace and use the existing duct system. We’ve done a number of similar projects and have seen similar performance.
In doing a lot of energy modeling, we’ve noticed that the value of R-value (pun intended) is severely overblown. The 1918 project has ⅓-½ the R-values of the super insulated TREE House, yet still outperforms it substantially.
Why? Heating and cooling (HVAC) is the biggest piece. Let’s look at that.
TREE House HVAC
- 30,000 BTU Lennox 14 SEER 8.5 HSPF multi split heat pump with 4 heads. One head on first floor, one head in each of the 3 upstairs offices.
- GE Geospring hybrid heat pump water heater which also heats heated basement floor
- Heat load 36,400 BTU/hr from REMRATE, presumed to include fudge factors
Like I said last time, the TREE House HVAC was done before I became proficient in it. The heat pump was undersized because originally a boiler was specified to heat the basement floor. The idea was that heat would rise through the house to heat the rest. That would have been problematic in this particular project because it’s so tight, there is very little stack effect which is what helps heat rise through a building.
A boiler was installed for basement floor heat, but it was supposed to be a “kombi” boiler that does both space heat and hot water. Unfortunately, the wrong one was installed, so we opted to remove the boiler entirely and replace it with a heat pump water heater. That allowed us to remove the gas meter, our first full electrification – many thanks to Dr. Debbie Kasper for the leap of faith on that one!
Unfortunately, this requires the resistance element in the heat pump water heater to carry much of the load of the house since the heat pump scavenges heat from inside the building, not outside.
If a larger more efficient heat pump had been used and one head was put in the basement, the energy use of the building would probably be similar to the 1918 House of the Future. When the basement is turned into a classroom, the plan is to add another mini split system there.
Here is the usage of the heat pump, represented by the dotted line below the overall usage line. You can see it’s the majority of the usage of the home.
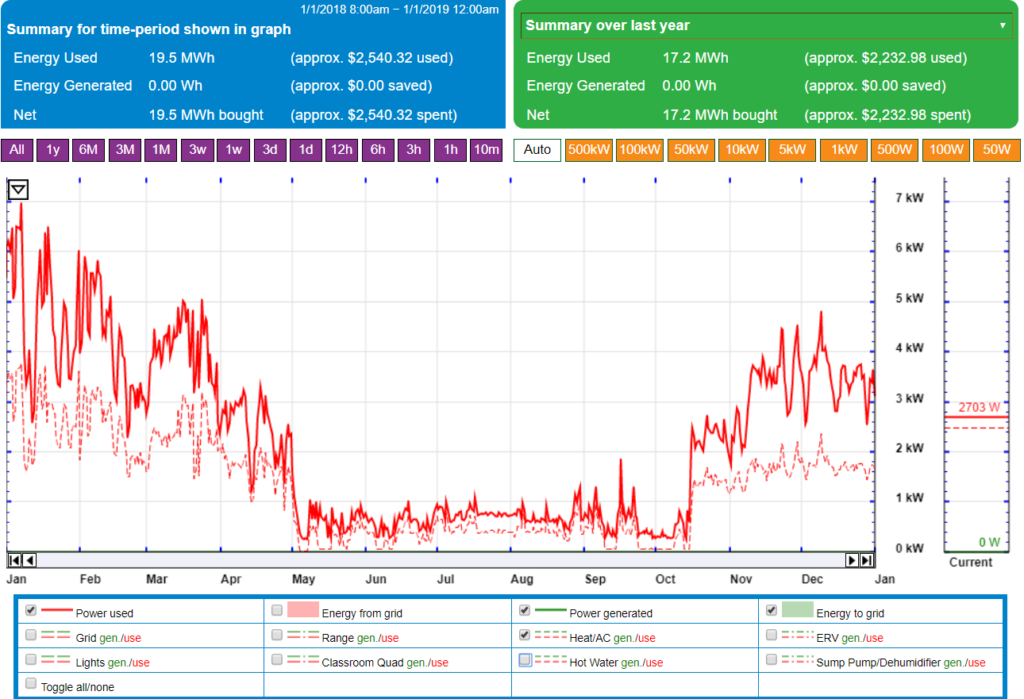
And here is the water heater which heats the basement floor:
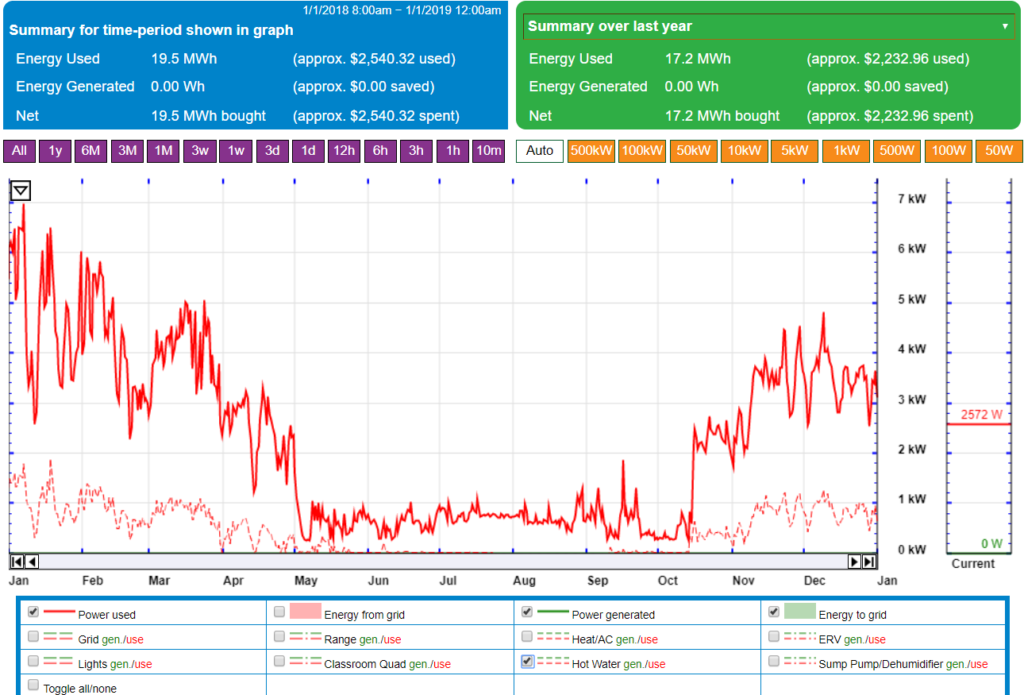
It’s difficult to extract the exact energy usage from eGauge energy monitor reports, but these two charts show that HVAC is the predominant energy user.
It should be noted that this mini split heat pump has mediocre performance amongst it’s brethren, better models are in the 10.5-11 HSPF range compared to the 8.5 for this one. It’s only a $1-2K cost difference, so a missed opportunity on a project with a high budget like this one.
1918 House of the Future HVAC
- 36,000 BTU Carrier GreenSpeed 21 SEER 13 HSPF ducted heat pump
- Resistance electric water heater
- Heat load 50,838 BTU from TREAT, which is close to Manual J, the industry standard. 27,000 for first and second floors only without fudge factors.
This project is one example being able to discount Manual J by 30-60% and still meet heating load on the coldest day. We see this again and again on our projects, it’s part of what lead us to like heat pumps so well – they have much smaller outputs that actually match the needs of our projects.
This particular heat pump is also capable of reheat dehumidification, a major part of BAD ASS HVAC. BAD ASS HVAC works for most new and existing homes in most climates, provides excellent comfort and IAQ, and happens to be all electric. I’ll introduce it early next year.
This system also offers whole house filtration to knock contaminants out of the air, something mini splits can’t do well. This particular home did not get fresh air capability though, which can be seen in Foobot air quality monitor reports.
Another nice thing about the Carrier GreenSpeed and its Wi-Fi thermostat is that you can track energy use by the day, month, and year, as well as by function – heating, cooling, backup heat, and reheat dehumidification.
This house has proven to be a miser, as you can see in this 11/9/19 screenshot.
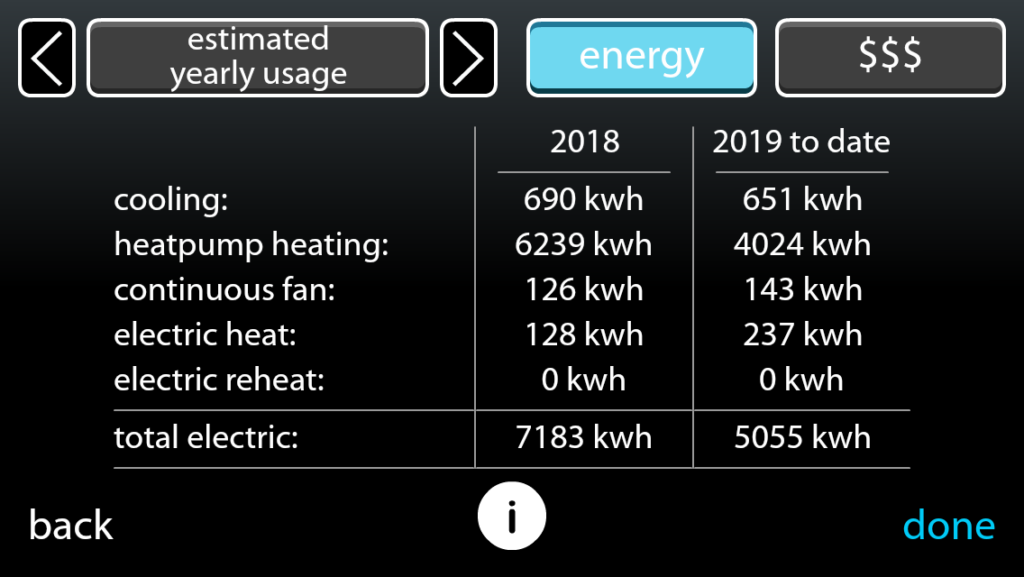
I have thousands of screen shots watching these heat pumps operate. They are remarkable machines. For reference, our old house used about 12,000 kwh/year PLUS 1800 therms of gas. (1,000 of that was the heat pump water heater, 3,000 was for charging my Chevy Volt.) This house is using 12,400 total without gas!
Market Implications
To me, this is the cool part. $150K demonstration projects are great, but they’re not scalable. This house is worth $200-225K, and this project didn’t add anywhere near the cost to its value. For a homeowner looking to retire someday, this is a poor use of capital.
The good news is that we don’t have to go anywhere near that far to get killer results. In fact, smaller projects can deliver better results, as you’ve seen.
While a $40K project is not inexpensive, it’s less than a typical kitchen remodel. We find that effective projects can be done for $100-200/month or $15-30K, which many households can afford.
More importantly, these projects help solve problems consumers care about like hot and cold rooms, mold, reducing asthma and allergies, and more. Every client has different concerns and budget constraints, and every house has different needs. You have to solve for all three to get a viable project.
Creating viable projects at scale is a serious challenge, frankly one that no one has figured out yet. We’re working on it though, and we think we’re very close. We’ve been developing a system for this called HVAC 2.0 (recently renamed from Home Performance 2.0.) If you want to learn more join us in the HVAC 2.0 Development group on Facebook, a number of the best HVAC contractors in the country already have.
In the meantime, I hope this series has helped you to question traditional deep energy retrofits. They have their place and they’ve taught us a lot, but we can get similar, often better, results with much less deep projects that have a real chance at scale.
Nate Adams is the founder of Energy Smart Home Performance in Cleveland Ohio and of NateTheHouseWhisperer. com. Rather than focus on energy efficiency, Nate focuses on solving the root causes of client problems like uncomfortable rooms, mold, wet basements, and icicles. As a fan of radical transparency, he has published the most detailed case studies in the industry on these projects.
Nate is currently writing The Home Comfort Book, a guide showing people how their homes really work and how to truly solve problems, instead of putting band-aids on bullet wounds. It is meant to create consumer demand for this work rather than the traditional supply focus that has been taken for forty years.
His writing has been published in numerous outlets including GreenTech Media, CleanTechnica, the Journal of Light Construction, Green Building Advisor, and more. Learn more at: http://energysmartohio.com/
The post The TREE House, Part 2: appeared first on Healthy Indoors.